Managing a Bill of Materials (BOM) with data analytics
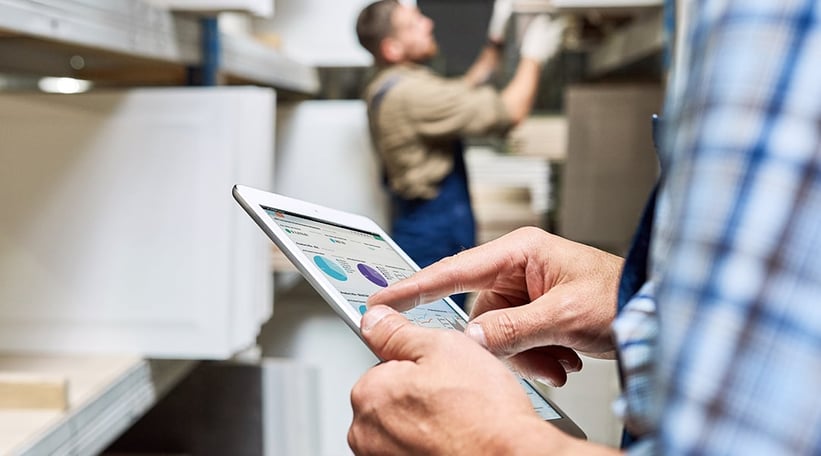
What is a Bill of Materials (BOM)?
A Bill of Materials (BOM) is a comprehensive list of all necessary materials and components required to manufacture a finished product. To be effective, a BOM includes raw materials, quantities of components in the assembly process, and spare parts for repair. Many companies, especially those that both manufacture and sell products, struggle to consolidate all this material requirements planning. Component reporting using data analytics is a simple way to tackle BOM challenges, gain clarity, and streamline supply chain and procurement processes.
A Bill of Materials (BOM) plays a critical role in multiple aspects of manufacturing and business operations like sales. For product costing, the BOM provides a detailed breakdown of materials and components, enabling accurate cost estimation and pricing strategies. In product lifecycle management (PLM), the BOM tracks changes and revisions, ensuring alignment across design, manufacturing, and end-of-life stages. For production planning, it serves as a blueprint for assembling products, improving efficiency and minimizing errors. In supply chain management, the BOM helps optimize procurement and inventory levels by identifying the materials required and their lead times, ensuring smooth production flow and reducing delays.
The challenge of managing a manufacturing Bill of Materials (MBOM Data)
Many years ago, a Phocas employee Ed, who had worked as an IT manager at an original equipment manufacturer (OEM) of computer parts, shared his struggle with managing Manufacturing BOM (MBOM) data effectively. This challenge led Phocas to develop a solution using data analytics to address MBOM management.
For example, Ed dealt with numerous parts for laptops. Laptops are made up of components such as: chassis, motherboard, optical drive, display, keyboard, graphics card, printed circuit board
Each component had different failure rates, and each laptop comprised a different combination of these components, often in varying quantities. From this experience, the Phocas development team realized that component reporting within the manufacturing process could be efficiently managed using Phocas and customers enterprise resource planning systems in the manufacturing industry.
Evolution of MBOM reporting
Initially, MBOM reporting in Phocas was simple, where one item (the parent) consisted of multiple parts (the children). This parent-child relationship was displayed neatly in Phocas. Each MBOM was effectively a transaction, similar to a sales invoice, consisting of individual parts.
This concept evolved into a more complex MBOM structure, where parent items could have children, and those children could be parents themselves. For example, a laptop has a motherboard, optical drive, and keyboard, while a motherboard comprises components like a USB, a Parallel port, and a CPU chip. Using a sales database and inventory database, Phocas users can now easily create a component dashboard.
Types of Bills of Materials
There are various types of BOMs that companies use, depending on their needs.
Engineering Bill of materials (engineering bom): a detailed list of components, sub-assemblies, and materials designed during the product's development phase, typically created using computer-aided design (CAD) software. It reflects the product's design intent, including part numbers, descriptions, and specifications, serving as the foundation for manufacturing and procurement processes.
- Single-level BOM: a straightforward list of components needed to assemble a product.
- Multi-level BOM: a detailed BOM showing components and sub-assemblies, illustrating the hierarchical relationship between parent and child components.
- Configurable Bill of materials (CBOM or configurable BOM): A flexible BOM that allows for customization based on specific customer requirements.
Sales Bill of materials: the components and sub-assemblies that make up a product, as sold to the customer, and specifies how they are delivered. Unlike other BOMs, the SBOM reflects the product's composition at the point of sale, listing both the final product and its individual parts for order processing and delivery.
Component reporting with Phocas
Component reporting is how Phocas simplifies complex and time-consuming tasks like managing BOMs. Phocas business intelligence consolidates various data sources into one dashboard, providing a clear picture of components and a bom structure.
A dashboard example provides visibility into component usage, answering questions about what components need to be purchased based on orders. The main widget, 'Components to be ordered,' integrates all dashboard information, indicating that 16 components need to be ordered based on usage and orders.
Factors contributing to the components to be ordered include:
- Components with adequate stock
- Production required for stock
- Production required for orders
- Components on Purchase Order (PO)
- Products with less than one month coverage
- Products on Sales Order (SO)
- Components needed on overdue SO
Clicking on the 'components to be ordered' widget leads to a detailed list of components to be ordered, including lead times. This helps the procurement team order the right amount of components, reducing deadstock and adjusting for seasonality.
Rivertrace case study
Rivertrace, a manufacturer based in Surrey, England, uses data analytics to enhance reporting, control component usage, and manage its MBOM template. Operations Director Martin Saunders explains how Rivertrace benefits from Phocas data analytics.
Saunders identified a need for live reporting from its MRP/ERP system, Merlin. While Merlin handles transactional data well, Saunders wanted a dashboard for an overview of all areas of the production process. Phocas, integrated with Merlin, provided the reporting he needed.
Saunders appreciates having consolidated data accessible from anywhere in the cloud. Data analytics help Rivertrace make better inventory management and stronger materials management decisions. It also helps identify and address business issues quickly.
Rivertrace manages over 7,000 components and struggled to determine component demand. Designing everything in SolidWorks, which creates an MBOM imported into its MRP system, Rivertrace faced challenges managing lower-level components, so needed a multi-level Bill of Materials.
Phocas integrated with Merlin MRP/ERP, provides up-to-date data, displaying the product structure meaningfully. It allows Rivertrace to create alerts and favorites on components, suggesting what to purchase and calculating supplier lead times to avoid delays.
Effective BOM management is crucial for manufacturing and selling products. Data analytics, like Phocas, simplifies BOM management, providing clarity and efficiency. By consolidating data into a single dashboard, companies can reduce deadstock, adjust for seasonality and improve operations.

Empowering businesses with intuitive data analytics, driving informed decisions for growth and profitability. We make people feel good about data.
Related blog posts
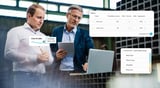
Tariffs are here. Whether you're in manufacturing, distribution or retail, it's important to understand how importing from affected countries such as Canada, Mexico or China or chosing local production, can affect your bottom line. We want to encourage you to scenario plan now not retrospectively.
Read more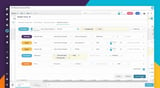
For finance teams in manufacturing, distribution or retail, effective demand planning is critical to meeting customer expectations without tying up cash in excess inventory. When done right, it ensures the right products are available at the right time and in the right quantities.
Read more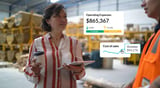
In today’s fast-paced business world, operational efficiency and confident decision-making are key to keeping your competitive edge. However, leveraging financial and operational data to do just that is a significant challenge for many organizations.
Read more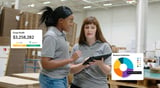
Sales and operational planning (S&OP) helps businesses to align their strategic goals with day-to-day operations. By integrating financial planning with operational and sales planning, S&OP ensures that all departments work cohesively towards common objectives. This process operates on strategic and tactical levels, providing insights that influence long-term decisions while guiding day-to-day actions. Understanding the dual focus of S&OP is essential for creating a robust plan that addresses immediate needs while positioning the company for future success.
Read moreBrowse by category
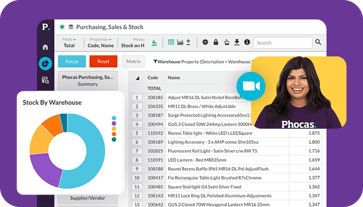
Find out how our platform gives you the visibility you need to get more done.
Get your demo today